BBB MAGAZINE
CREDIT
-
- ライター
- 執筆
NANDY小菅
-
- 撮影
NANDY小菅
-
- バイク
GSX1300BK B-KING

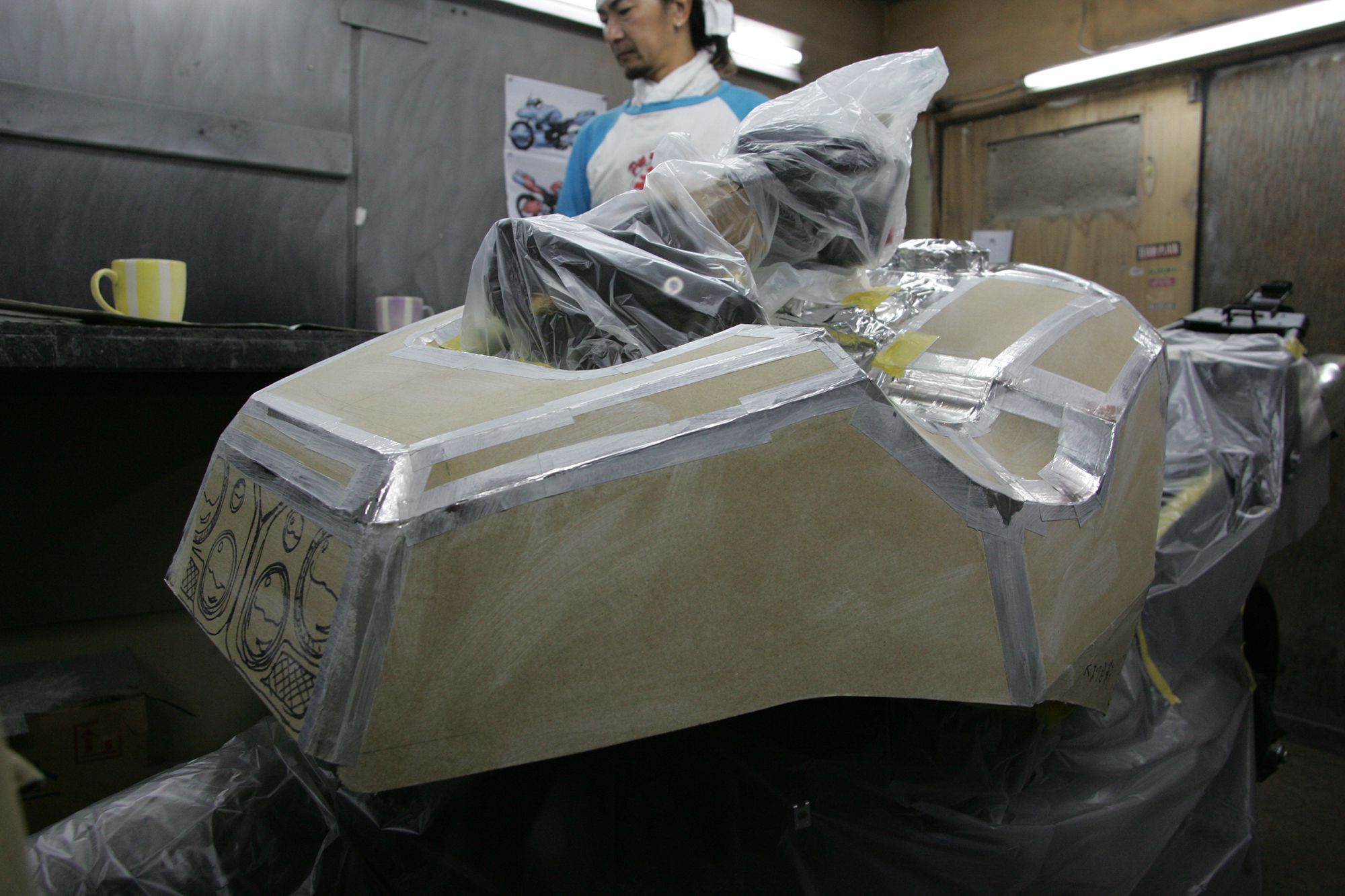
これが前回までボール紙で製作してきたカウルの原型となるもの。ボール紙の隙間にはアルミテープを貼って、表面にはワックスが塗られていますが、これは樹脂が染みこまないようにするためと、樹脂が硬化した後でボール紙が剥がれやすくするため。
ボール紙原型からFRPに!
まずはタンクの後ろ側から貼っていくことにしました。ガラス繊維を適度な大きさに切って合わせてみます。その際、別の繊維と重なる部分には繊維が絡まりやすくするために縁をほぐしておくと良いでしょう。
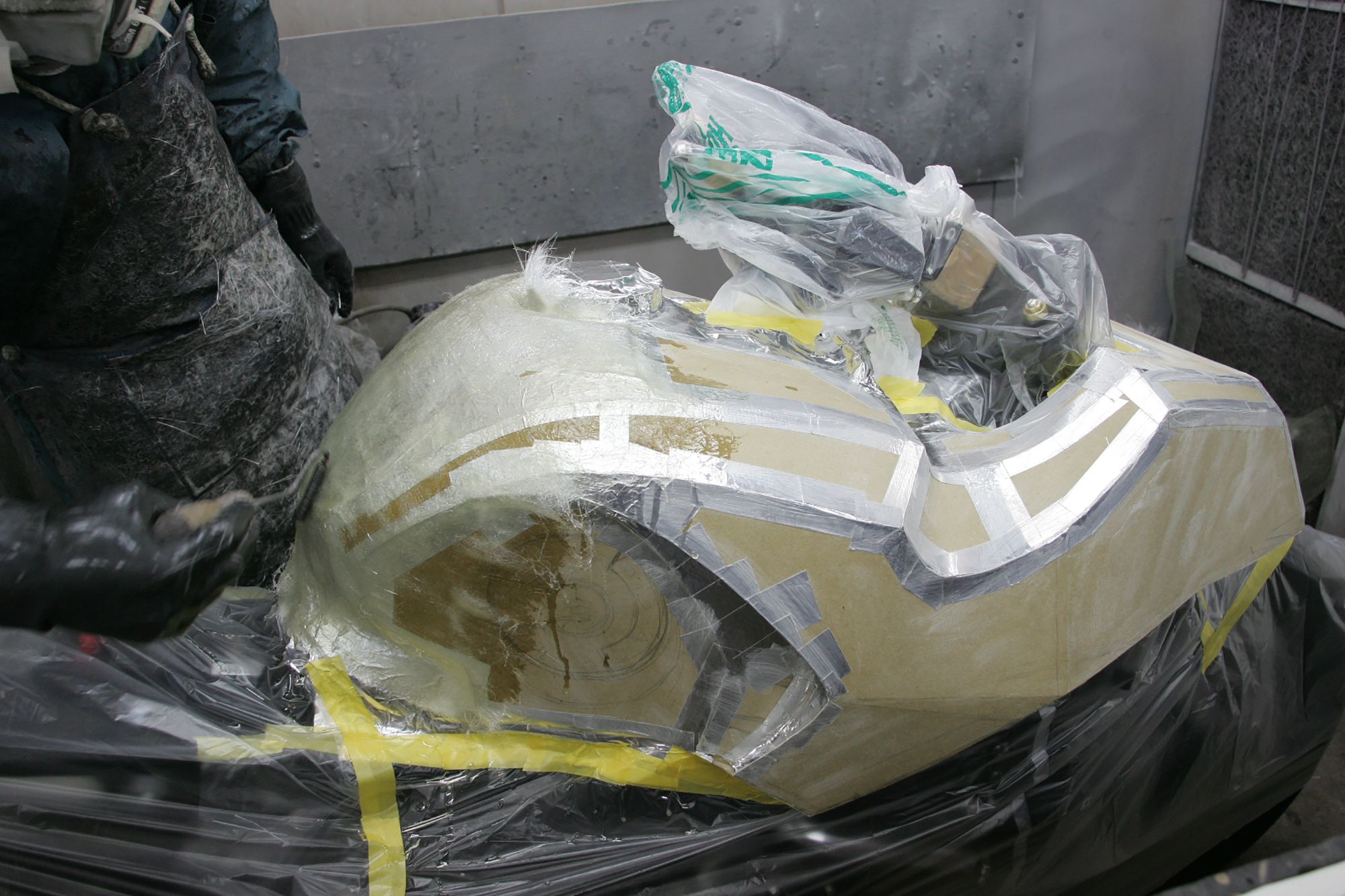
脱泡ローラーを使用して、樹脂やガラス繊維の間に入っている空気を抜いていきます。この作業をきちんとやるかやらないかで、美しく抜けるかどうかが決まる、地味ですが大事な作業です。
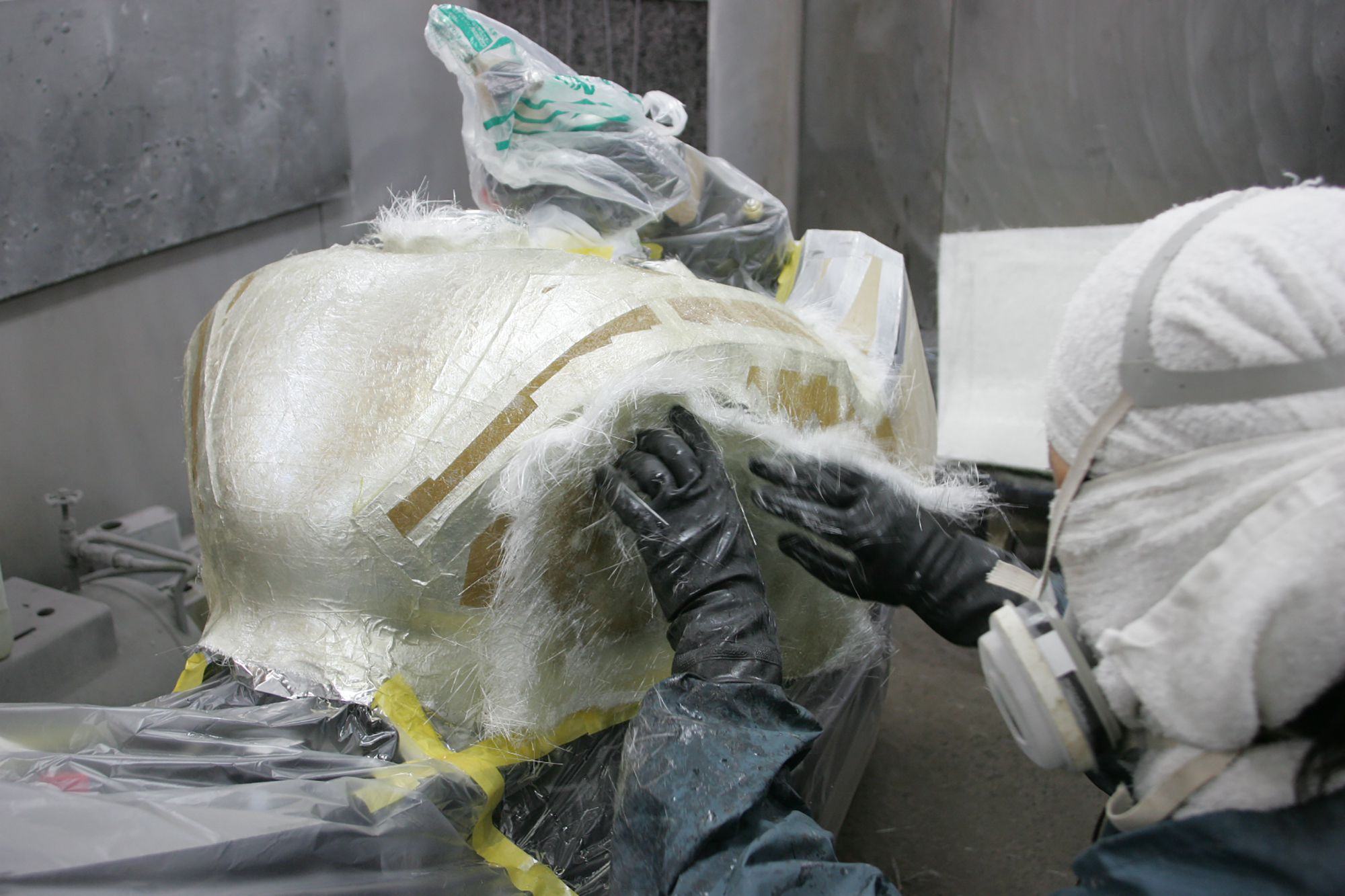
続いてはサイド部分の貼り込みに移ります。サイド部分には逆アールが付いているのでそういった部分は要注意箇所です。もしやりにくければ、先にガラス繊維は樹脂を付けてしまってから型に貼り付けてもOKです。
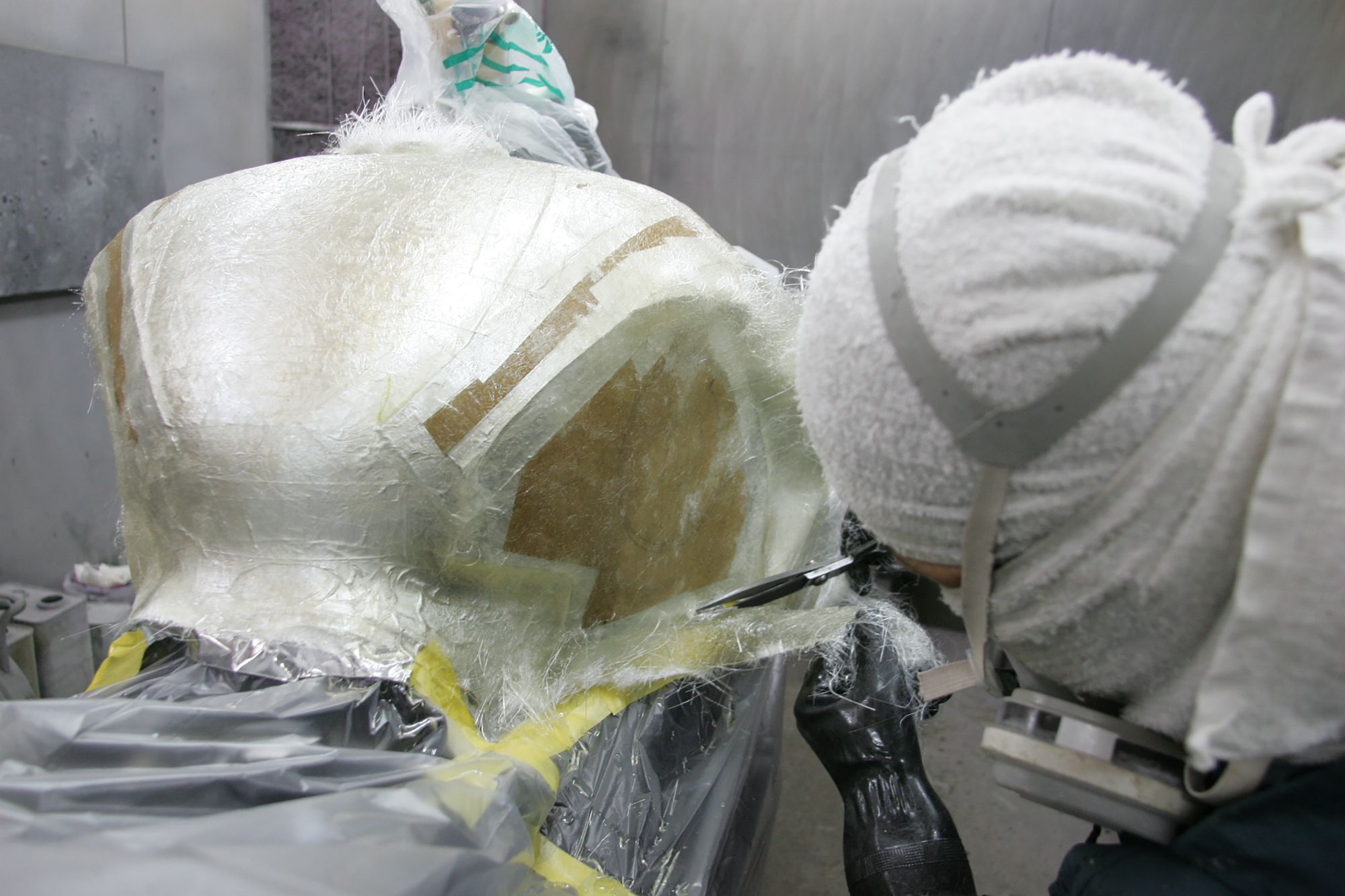
縁などの不必要な部分はこの時点でカットしてしまってもかまいません。特にこういった箇所の場合、樹脂によって重くなってしまって、逆アール部分が引っ張られてしまいガチなので、切ってしまうのが得策。
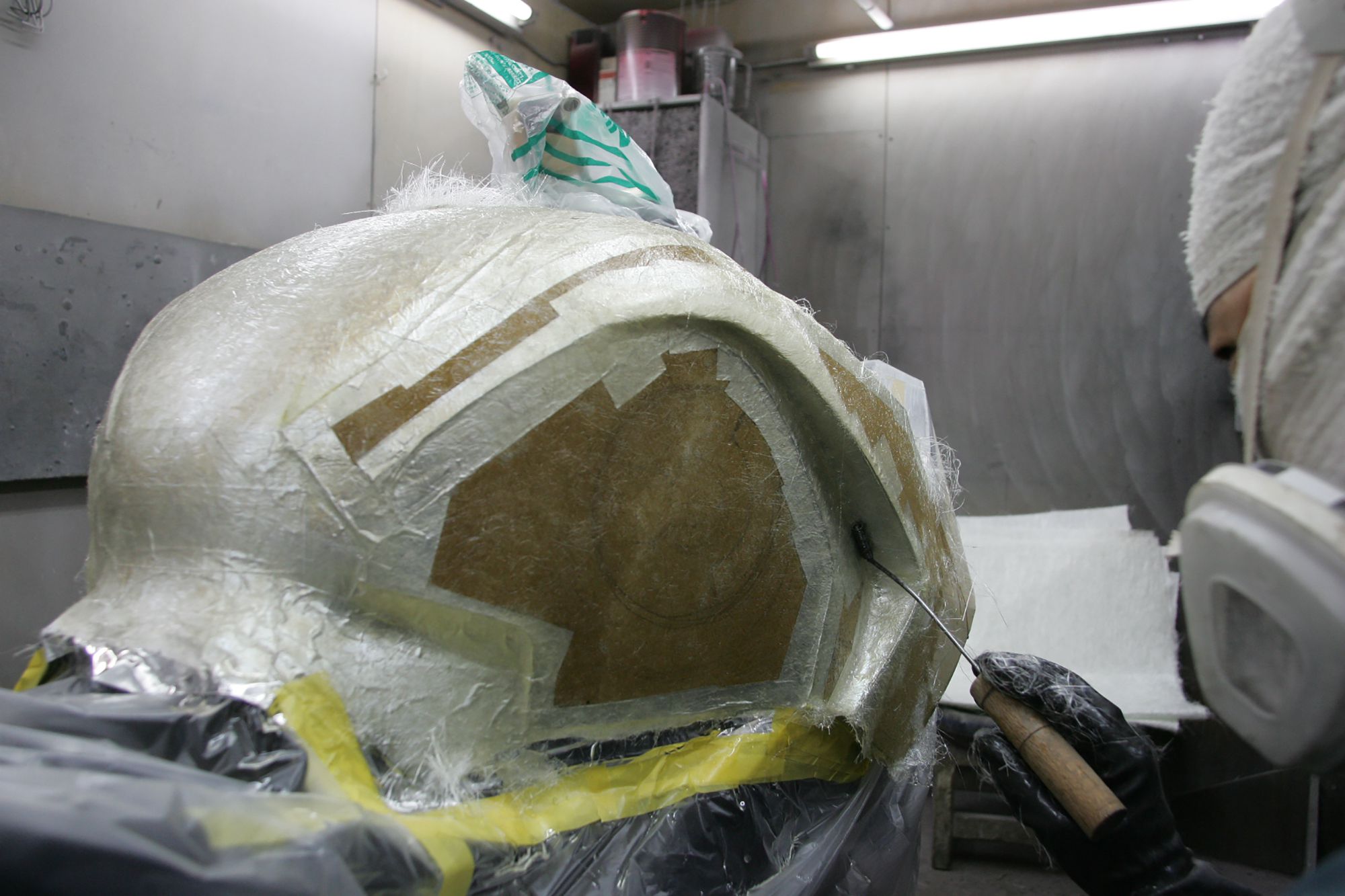
ダクト内側の逆アールは最も貼り難い部分。脱泡ローラーを巧みに駆使してエアを抜きつつ型に押し当てていきます。プロフェッショナルなテクニックの見せ所!
サイドまで貼れた時点で再びタンク後方に戻り、2枚目を貼ってしまうことにしました。2枚貼るのは強度を出すため。なお、ガラス繊維にも目の粗さなどがあり、今回は#600を2枚貼りで行くことにしました。
作業は引き続き、前側の方へと進行していきます。ガラス繊維を切って貼って、樹脂を塗って脱泡ローラーで空気抜いて・・・という作業の繰り返しですが、ここまでの境地に至るまでには無論、職人技が編み込まれているワケです!
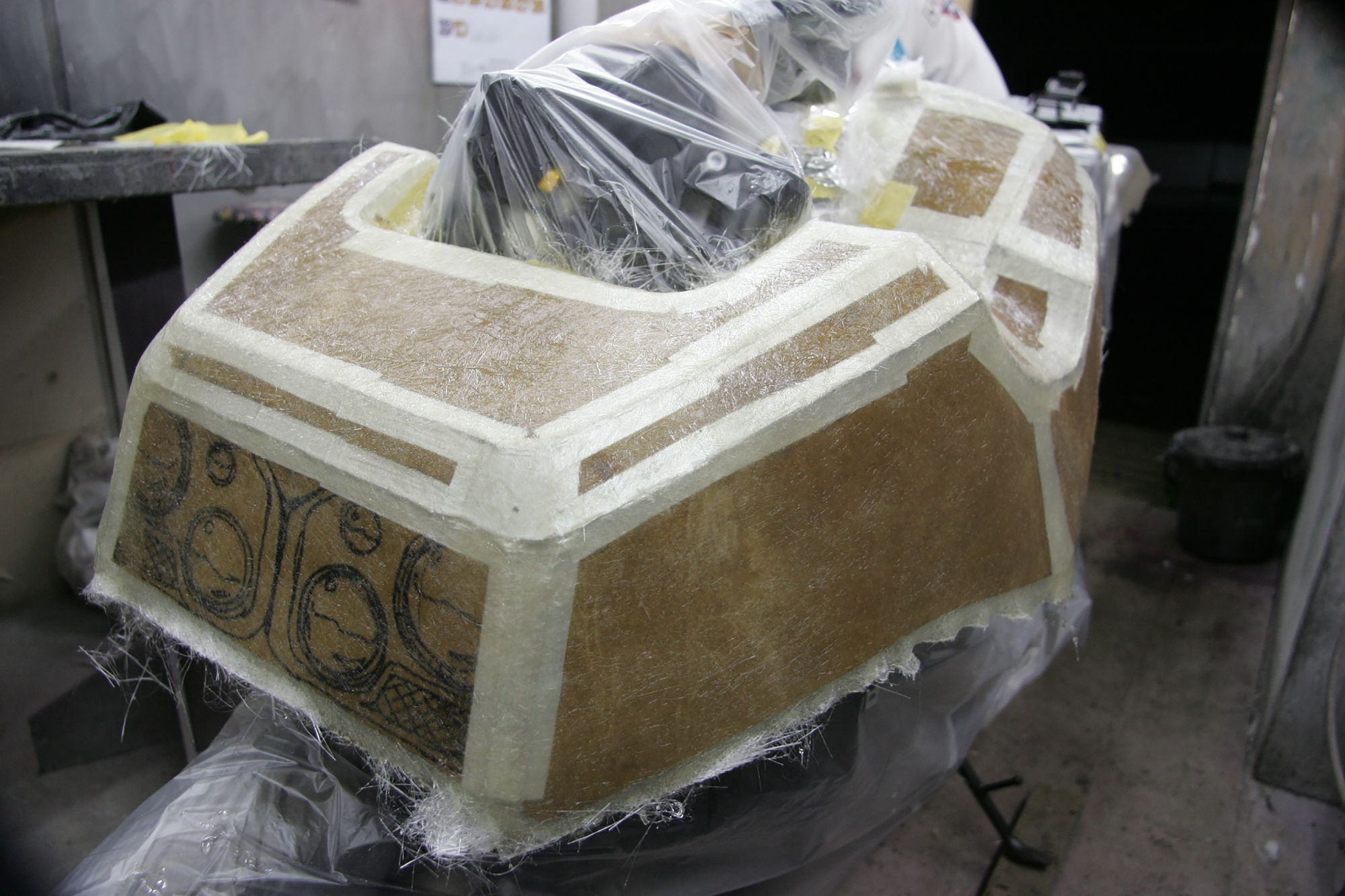
全てを貼り終えました~。まだ貼り立てなので硬化するまでちょい待ちな状態です。あとは硬化を待って、内側のボール紙を剥がせば・・・カウルの大ざっぱなFRP原型の完成です
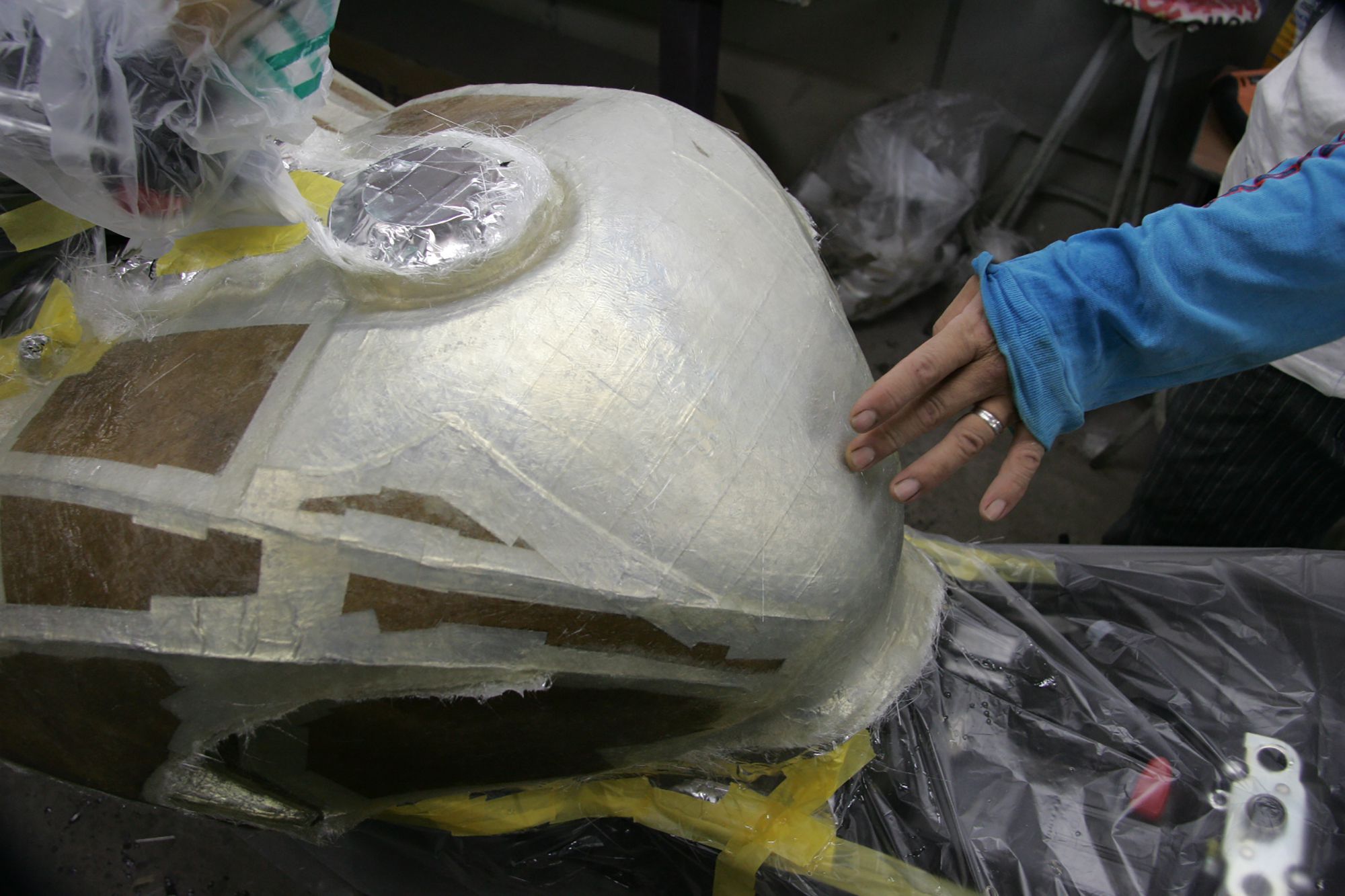
貼り立てと言っても最初に貼り始めたタンク後方などは、既にかろうじて触れる程度には硬化が始まってましたけどね。

人気コンテンツ
-
BBB Staff BLOG
2021.03.17
販売証明書の書き方を掲載!原付二種ナンバープレートは市役所で取得できます
新型コロナウイルスの感染拡大に伴い、三密を避けることができる手段として注目を浴びているバイク。そ...
-
BBB Staff BLOG
2019.05.31 / Vol.22
【2019年版】ミニカー登録まとめ
BBBマガジンの記事ではミニカー登録についてキーワード検索されているのが多く、需要がありそうだったのでミニカー登録につい...
-
BBB Staff BLOG
2020.11.11
実は簡単⁉市役所に行くだけで完結 原付一種ナンバープレート取得までの手順をご紹介
近年、EVモビリティやキックボードなどが登場し、若者を中心に多くの人から注目を集めている原付一種(50㏄)。けれども、意...
-
大人のたしなみとしてベスパに接してみよう!
2015.06.03 / Vol.12
スモールで遊ぶ #01
さてさて今回からいよいよ「スモールで遊ぶ編」をお届けしますよ〜......って、スモールってなに? となっちゃいますよ...
-
レストア野郎★Zippy編
2014.01.11 / Vol.05
ホイールとエンジンを自家塗装してみよう! ペイント編
スポークホイールのペイントとなると、一度スポークをバラしてハブもリムも磨くのはもちろん、スポークも1本ずつ磨いてからの作...
-
プロトモスピーダ
2008.08.07 / VOl.09
アッパーカウル製作1
ボール紙を切って原型の元となる形状を作り上げていきます。出来上がったら上にFRPを貼っていくので、ボール紙といってもある...
-
レストア野郎★2番星★FTR250編
2014.10.28 / Vol.04
タペット調整でエンストするエンジンが快適になるとイイナ!
Vol.04 タペット調整しましょう! タペット調整とはカムシャフトとロッカーアームとの隙間であるバ...
-
BBB Staff BLOG
2018.09.20 / Vol.17
今こそ2ストに乗ろう!2018 〜2ストの魅力をどっぷり解説〜
オートバイは走るシチュエーションや、ネイキッド・クルーザー(アメリカン)・オフロード(モトクロス...
-
BBB Staff BLOG
2019.10.29
ツーリング動画を撮影したい!必要なものや撮影の手順を紹介!
ツーリングでは、自分の好きなルートを選び、バイクを走らせながら周囲に見えてくるさまざまな景色を楽しむことができます。そん...
BBBマガジン
この記事の日付(2008.09.04)に近いコンテンツ
-
藤原かんいち電動バイク世界一周 夢大陸オーストラリア編
「ついに踏み出した、はじめの一歩」
2008.11.23 更新 / Vol.02
-
藤原かんいち電動バイク世界一周 夢大陸オーストラリア編
「膨らむ地平線への思い」
2008.11.06 更新 / Vol.01
-
BBB Staff BLOG
ここがスゴイ! インジェクション搭載バイク
2008.10.27 更新 / Vol.05
-
BBB Staff BLOG
エコバイク特集! ガソリンが高い今こそバイク!
2008.08.27 更新 / Vol.04
-
BBB Staff BLOG
ファーストバイクはこれだ!
2008.06.27 更新 / Vol.03
-
BBB Staff BLOG
ツーリングのススメ!
2008.04.27 更新 / Vol.02